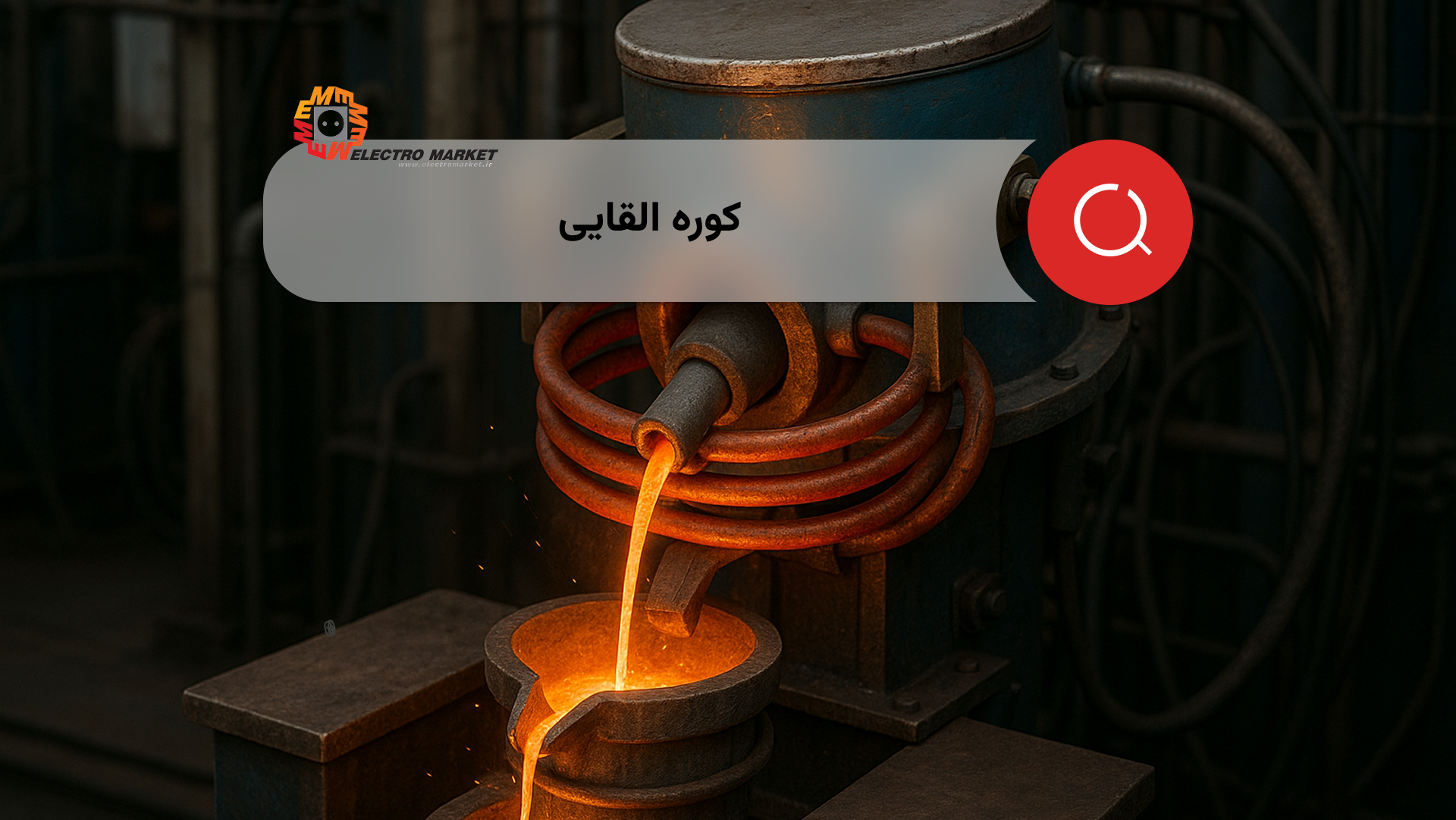
کوره القایی: راهنمای جامع تکنولوژی ذوب مدرن
کوره القایی به عنوان یکی از پیشرفتهترین و کارآمدترین روشهای ذوب فلزات، نقش حیاتی در صنایع متالورژی ایفا میکند. این فناوری که بر پایه اصول الکترومغناطیس بنا شده، مزایای بیشماری از جمله پاکیزگی، سرعت بالا و کنترل دقیق فرآیند ذوب را به ارمغان میآورد. در این مقاله از الکترومارکت، قصد داریم به طور جامع به بررسی ابعاد مختلف کورههای القایی بپردازیم و جزئیات فنی و عملیاتی آنها را مورد کنکاش قرار دهیم.
اجزای اصلی کوره القایی
به طور کلی، یک کوره القایی از بخشهای متعددی تشکیل شده است که هر یک وظیفه مشخصی را بر عهده دارند:
-
بوته (Crucible): این بخش شامل اسکلت فلزی کوره، کویلهای القایی، جداره نسوز، هسته ترانسفورماتور و سایر اجزای مرتبط است که مذاب را در خود جای میدهد.
-
تاسیسات الکتریکی: این مجموعه شامل تجهیزاتی نظیر دژنکتور، سکسیونر، ترانسفورماتور، مبدل فرکانس، خازنها، چوکها، کلیدها، کولرها، مکندهها و تابلوهای کنترل است که وظیفه تامین و تنظیم توان الکتریکی کوره را بر عهده دارند.
-
تاسیسات خنککننده: تجهیزات الکتریکی کوره القایی در طول زمان کارکرد، حرارت زیادی تولید میکنند که برای جلوگیری از آسیب دیدگی و حفظ عملکرد بهینه، نیاز به خنکسازی دارند. این خنکسازی میتواند از طریق فن، ایرکاندیشن یا کولر گازی صورت گیرد. همچنین، کویل و بدنه کوره در کورههای بوتهای، و پوسته اینداکتور، پوسته خنککن و گلویی کوره در کورههای کانالی، معمولاً با آب خنک میشوند. این بخش شامل مبدلهای حرارتی، پمپها و برجهای خنککننده است که سیستم گردش آب را مدیریت میکنند.
-
تاسیسات حرکت بوته: برای تخلیه مذاب از کوره، سیستمی جهت حرکت بوته در نظر گرفته شده است. این سیستم در کورههای بزرگ معمولاً هیدرولیکی (شامل جکهای هیدرولیک، پمپ، مخزن روغن و شیرآلات) و در کورههای کوچکتر مکانیکی یا هیدرولیکی است.
-
محل استقرار کوره: این بخش شامل فضای فیزیکی استقرار بوته (pit furnace)، فونداسیون، چاله تخلیه اضطراری، و محل قرارگیری تاسیسات الکتریکی، هیدرولیکی و خنککننده، به همراه تابلوهای فرمان و کنترل.
-
تاسیسات تهویه: این تاسیسات، به ویژه در کورههای بوتهای بزرگ، برای جمعآوری و حذف دود و غبار ناشی از فرآیند ذوب، از اهمیت بالایی برخوردارند.
هر یک از این بخشها نیازمند برنامهریزی دقیق برای تعمیر و نگهداری هستند که جزئیات آن بسته به نوع کوره (کانالی یا بدون هسته)، ظرفیت، فرکانس و نوع جداره نسوز میتواند متفاوت باشد. برای اطلاعات بیشتر در مورد نگهداری از تجهیزات صنعتی، میتوانید به مقالات دیگر در وبلاگ الکترومارکت مراجعه کنید.
اصول کار کوره القایی
عملکرد کوره القایی شباهت زیادی به یک ترانسفورماتور دارد. در این سیستم، سیمپیچ کوره نقش سیمپیچ اولیه را ایفا میکند و بار کوره (فلز مورد نظر برای ذوب) به عنوان سیمپیچ ثانویه عمل میکند. جریان متناوب عبوری از سیمپیچ اولیه، یک میدان مغناطیسی متغیر ایجاد میکند که به نوبه خود جریانهای گردابی بسیار بزرگی را در بار کوره القا میکند. این جریانهای گردابی، به دلیل مقاومت الکتریکی بار، حرارت زیادی تولید کرده و منجر به ذوب فلز میشوند.
نکته قابل توجه در کورههای القایی، وجود یک نیروی دافعه بین میدان القایی و جریانهای گردابی در مذاب است. از آنجا که سیمپیچ ثابت است، این نیرو باعث حرکت و همزدن مذاب میشود که خود یک مزیت بزرگ محسوب میگردد. همزدن مذاب به یکنواختی دما و ترکیب شیمیایی کمک شایانی میکند و امکان تولید آلیاژهای پیچیده را فراهم میسازد. فرکانس جریان با شدت همزدن مذاب رابطه عکس دارد؛ به این معنی که جریان با فرکانس پایینتر، همزدن شدیدتری را ایجاد میکند.
کورههای القایی از مزایای دیگری نیز برخوردارند؛ از جمله عدم وجود شعله یا گاز اکسیدکننده و همچنین عدم تماس مستقیم هوا با سطح مذاب، که منجر به کاهش آلودگی و حفظ کیفیت مذاب میشود.
دستهبندی کورههای القایی
کورههای القایی از نظر شکل و آرایش سیمپیچ به دو دسته اصلی تقسیم میشوند:
الف: کوره القایی کانالی یا هستهای
در کوره القایی کانالی (هستهای)، سیمپیچ کوره یا سیمپیچ اولیه در اطراف یک هسته آهنی لایهلایه قرار میگیرد که کانال حاوی مذاب را احاطه کرده و به بدنه کوره متصل است. شکل این کانال میتواند U، V یا W باشد که بسته به طراحی و نوع آلیاژ مورد ذوب، متفاوت است.
این نوع کورهها مستقیماً به برق شهر (فرکانس ۵۰ یا ۶۰ هرتز) متصل میشوند. حرارت مستقیماً در کانال به فلز منتقل میشود و نیروی مغناطیسی باعث گردش مذاب بین کوره اصلی و کانال میشود. دمای فلز در کانال میتواند تا ۵۰ درجه سانتیگراد بالاتر از دمای مذاب در بدنه کوره باشد.
کورههای القایی کانالی معمولاً نمیتوانند با شارژ سرد (قراضه خشک) شروع به کار کنند، زیرا فلز در کانال باید مذاب باشد. به همین دلیل، پیش از شروع به کار با قراضه سرد، نیاز به پیشگرمایش با شعله گاز یا نفت برای ایجاد مذاب اولیه وجود دارد. این ویژگی باعث میشود که کورههای القایی هستهدار بیشتر به عنوان کورههای نگهدارنده مذاب یا واحدهای تولید حرارت زیاد برای کورههای ذوب دیگر مورد استفاده قرار گیرند. برای کاهش هزینهها، اغلب در طول روز با توان کامل کار میکنند و در شب با کاهش توان، به عنوان نگهدارنده مذاب مورد استفاده قرار میگیرند. کاربرد این کورهها به عنوان واحد ذوب، محدود به آهن و فلزات غیرآهنی است که مسئله جذب گاز در آنها (مانند فولادها) مشکلساز نیست؛ زیرا دمای کانال میتواند از ۱۵۰۰ درجه سانتیگراد فراتر رود.
ب: کوره القایی بدون هسته
کورههای القایی بدون هسته از رایجترین انواع کورههای القایی هستند و برای ذوب طیف وسیعی از فلزات و آلیاژها کاربرد دارند.
عوامل موثر بر عملکرد کوره القایی
راندمان و طول عمر یک کوره القایی به عوامل متعددی بستگی دارد که مهمترین آنها عبارتند از:
-
اجرای دقیق برنامه تعمیر و نگهداری کوره: هر کوره القایی، بسته به نوع (کانالی یا بدون هسته)، ظرفیت، فرکانس، سیستم خنککننده و نوع جداره نسوز، نیازمند یک برنامه تعمیر و نگهداری دقیق و منظم است. رعایت این برنامه برای حفظ سلامت و بهرهوری کوره ضروری است. الکترومارکت به شما توصیه میکند که برای افزایش عمر مفید و بهرهوری تجهیزات خود، همواره به برنامههای نگهداری پیشگیرانه پایبند باشید.
-
شارژ مناسب: برای کورههای القایی بدون هسته که با فرکانسهای پایینتر از ۱۵۰ هرتز کار میکنند و تمام مذاب خود را تخلیه نمیکنند تا زمان شارژ بعدی کوتاهتر شود، لازم است مواد شارژ عاری از روغن و رطوبت باشند. وجود رطوبت و روغن میتواند منجر به پاشش مذاب و قطعات شارژ جامد به بیرون از کوره شود. علاوه بر این، مواد آلی باعث تولید دود در کارگاه میگردند. در کورههای القایی، سرباره معمولاً سردتر از مذاب است، که این امر توانایی کوره در احیای مواد اکسیدی را کاهش میدهد. بنابراین، این کورهها نمیتوانند مقادیر زیادی از مواد اکسیدی، خاک و سرباره را تحمل کنند و وجود مقادیر زیاد مواد غیرفلزی غیرآلی میتواند به ایجاد “پل” بالای مذاب، به خصوص در هنگام سرد بودن مذاب، منجر شود که مشکلاتی را در عملکرد کوره ایجاد میکند. ابعاد نامناسب شارژ نیز میتواند مستقیماً به جداره نسوز آسیب رسانده و به تشکیل پل روی مذاب کمک کند.
-
اپراتوری صحیح: در کورههای القایی بدون هسته، به ویژه با فرکانسهای پایینتر، چرخش و تلاطم مذاب به تولید ذوب با آنالیز و دمای همگن کمک میکند. اپراتور کوره (کورهدار) باید اصول خاصی را برای افزایش راندمان و حفظ سلامت کوره رعایت کند. این اصول شامل انتخاب شارژ مناسب، تنظیم دمای صحیح ذوب در مراحل مختلف، شارژ صحیح کوره، اضافه کردن به موقع و به مقدار معین مواد آلیاژی و افزودنی، توجه به تابلوهای کنترل و ابزارهای هشداردهنده، و رعایت کامل مسائل ایمنی است. جزئیات اپراتوری بسته به نوع و ظرفیت کوره، نوع ذوب تولیدی و نوع شارژ مواد جامد متغیر است. معمولاً سازنده کوره، دستورالعملهای کاملی برای تعمیر و نگهداری و اپراتوری صحیح ارائه میدهد که رعایت آنها برای عملکرد بهینه و طولانیمدت کوره حیاتی است.
-
وضعیت جداره نسوز: جداره نسوز کورههای القایی ممکن است بر اثر سایش مکانیکی توسط مذاب و شارژ جامد، خوردگی شیمیایی توسط سرباره، مذاب و اتمسفر کوره، شوکهای مکانیکی و حرارتی، کندگی و انهدام ناشی از برخورد با شارژ جامد، یا شیوههای نامناسب شارژ و ابعاد نامتناسب آن، آسیب دیده یا نازک شود. همچنین نصب و پخت نادرست جداره یا هرگونه انفجار داخلی نیز میتواند به آن آسیب برساند. از سوی دیگر، رسوب مواد غیرفلزی غیرآلی بر جداره میتواند باعث ضخیم شدن آن گردد. هر دو حالت (نازک یا ضخیم شدن جداره) برای کوره مضر است. نازک شدن جداره، هرچند در ابتدا ممکن است توان گرمایی کوره را افزایش دهد، اما در مجموع عمر جداره را کاهش داده و گاهی منجر به توقفهای ناخواسته میشود. ضخیم شدن جداره نیز راندمان کاری کوره را کاهش داده و میتواند در فرآیند شارژ اختلال ایجاد کند. برای درک علل این تغییرات، شناخت ترمومتالورژی مذاب، سرباره، اتمسفر کوره و آستر نسوز ضروری است. به عنوان مثال، وجود اکسیدهای قلیایی در ذوب آلومینیوم در کورههای با جداره آلومینایی، باعث اکسیداسیون آلومینیوم مذاب و رسوب آلومینا بر جداره و در نتیجه ضخیم شدن آن میشود؛ در حالی که همین اکسیدها در کورههای با جداره سیلیسی، موجب خوردگی شدید آستر نسوز میگردند.
کنترل خوردگی و سایش در کوره القایی
جداره کورههای بوتهای بسته به شرایط کاری، نوع جداره (شیمیایی و فیزیکی)، نحوه نصب، رطوبتگیری و پخت آستر، نوع و کیفیت شارژ جامد و نحوه شارژ، میتواند در حین کار ضخیم یا بر اثر سایش، فرسایش و خوردگی شیمیایی نازک شود. نازک شدن جداره به معنای نزدیک شدن مذاب به کویل و ضخیم شدن به معنای دور شدن مذاب از کویل است.
با نازک شدن جداره و نزدیک شدن مذاب به کویل، فوران مغناطیسی جذب شده توسط کویل افزایش یافته و در نتیجه آمپری که توسط کویل کشیده میشود، بالا میرود. بنابراین، اگر مقدار آمپر کشیده شده توسط کویل در یک ولتاژ معین و حجم مذاب مشخص (با فرض دمای تقریباً یکسان برای مقایسه، و در فرکانس مشخص برای کورههای متغیر) با حالت جداره نو مقایسه شود، افزایش آمپر مشاهده خواهد شد. این افزایش آمپر، نشاندهنده جذب بیشتر فوران مغناطیسی توسط مذاب است که باعث افزایش خاصیت سلفی مدار میشود و ضریب توان () از مقدار ایدهآل (یک) به سمت خاصیت سلفی منحرف میگردد. برای اصلاح ضریب توان، نیاز به خازن بیشتری در مدار خواهد بود.
روشهای پایش جداره
بهترین راه برای کنترل خوردگی جداره در زمانی که مذاب داخل کوره است، مشاهده و مقایسه مقدار جریان الکتریکی کشیده شده توسط کویل، ضریب توان و مقدار خازنهای مدار با حالت جداره نو است. عکس این مطالب در مورد ضخیم شدن جداره صادق است؛ با ضخیم شدن جداره، مذاب از کویل دور شده و حجم فوران مغناطیسی جذب شده توسط مذاب کاهش مییابد. در نتیجه جریان کشیده شده توسط کویل کم میشود و مدار خاصیت خازنی پیدا میکند، که ضریب توان از یک به سمت خازنی منحرف میسازد. برای اصلاح $ \text{cos } \alpha $، نیاز به حذف مقداری خازن از مدار است. بنابراین، با کنترل مداوم آمپر کشیده شده توسط کویل، ضریب توان و مقدار خازن در مدار، میتوان نازک یا ضخیم شدن جداره را تشخیص داد.
همچنین، مقاومت حمام مذاب (بر حسب اهم) در زمان پر بودن کوره و دمای کارکرد، شاخص مهمی است. کاهش مقاومت حمام نشاندهنده نازک شدن جداره و نزدیک شدن مذاب به کویل است و افزایش آن به معنای ضخیم شدن جداره و دور شدن مذاب از کویل. معمولاً اگر مقاومت حمام ۱۵ درصد کاهش یابد، به این معنی است که جداره نسوز نیاز به تعمیر دارد.
با نازک یا ضخیم شدن جداره، تعادل فاز کوره نیز تغییر میکند و مقدار خازن مورد نیاز برای متعادلسازی فازها نیز تغییر مییابد. علاوه بر این، با خوردگی یا ضخیم شدن جداره، مقدار حرارت منتقل شده به کویل تغییر میکند و در نتیجه اختلاف دمای آب ورودی و خروجی کویل نیز تغییر خواهد کرد؛ با نزدیک شدن مذاب به کویل، این اختلاف دما افزایش و با دور شدن، کاهش مییابد. با این حال، از آنجا که عوامل دیگری نیز بر دمای آب موثرند، این پارامتر به تنهایی کافی نیست و باید در کنار پارامترهای الکتریکی فوقالذکر مورد استفاده قرار گیرد.
اهمیت سیستمهای ایمنی
در برخی کارخانجات، این تصور اشتباه وجود دارد که اهممتر، نزدیک شدن مذاب به کویل را نشان میدهد. در صورتی که اهممتر مقاومت الکتریکی جداره را تعیین میکند. جداره سالم، حتی با ضخامتی کمتر از ۰.۵ ضخامت اصلی، دارای مقاومت الکتریکی به اندازه کافی بالایی است که اهممتر نتواند آن را تشخیص دهد. اهممتر تنها زمانی وضعیت خطر را نشان میدهد که جداره خیس باشد یا بر اثر نفوذ مذاب، اتصال کوتاه ایجاد شده باشد. در چنین حالتی (چه از خیس شدن جداره و چه از اتصال کوتاه)، باید بلافاصله کوره تخلیه شده و برای رفع عیب اقدام گردد. لازم به ذکر است که در زمان پخت جداره، مقاومت الکتریکی آن به دلیل وجود رطوبت، پایین است که این مورد با موارد خطر متفاوت است. بنابراین، اهممتر خوردگی جداره را مستقیماً نشان نمیدهد، بلکه نشاندهنده وضعیت ایمنی جداره است و در صورت هشدار، باید کوره بلافاصله تخلیه شود.
پایش دقیقتر وضعیت جداره
جهت کنترل نازک یا ضخیم شدن جداره در هنگام پر بودن کوره از مذاب، باید از ضریب توان () مدار، آمپر کشیده شده توسط کویل و مقدار خازن تصحیح بهره جست. مشخص است که در صورتی که خوردگی جداره موضعی باشد یا در ناحیهای خوردگی و در ناحیه دیگر افزایش ضخامت جداره رخ دهد، کنترلکننده ممکن است دچار گمراهی شود؛ زیرا خوردگی موضعی کوچک، هرچند خطرآفرین باشد، تأثیر چندانی بر آمپر کشیده شده توسط کویل ندارد و در صورت توأم بودن خوردگی و ضخیم شدن در نواحی مختلف، اثرات یکدیگر را خنثی میکنند. بنابراین، جهت کنترل دقیقتر وضعیت جداره میتوان از روشهای دیگری نیز استفاده کرد.
در کورههای با فرکانس بالاتر از ۱۵۰ هرتز، از آنجا که مذاب کوره پس از آماده شدن کاملاً تخلیه میگردد، میتوان از مشاهده مستقیم برای تشخیص خوردگیهای موضعی بهره برد. در کورههای با فرکانس خط و فرکانس سه برابر (۱۵۰ یا ۱۸۰ هرتز)، چون مذاب کوره کاملاً تخلیه نمیشود، مشاهده کامل کوره امکانپذیر نیست، اما قسمتهای فوقانی را میتوان مشاهده کرد.
خلاصهای از مدار الکتریکی کوره القایی بدون هسته
در بعضی از کورههای القایی، سیمپیچ از دو یا چند قسمت تشکیل شده است که هر یک میتوانند به طور مجزا یا با هم کار کنند. کورههایی نیز طراحی شدهاند که با دو فرکانس متفاوت کار میکنند: فرکانس بالا برای شروع کار و فرکانس شبکه برای ذوب پس از ایجاد مذاب اولیه.
ضریب توان برق با اتصال یک سری خازن به سیمپیچ کوره افزایش مییابد و با استفاده از خازنهای متغیر، میتوان توان برق را در طول فرآیند ثابت نگه داشت.
طبقهبندی کورههای القایی بر اساس فرکانس
کورههای القایی با توجه به فرکانس کارکردشان به دستههای زیر تقسیم میشوند:
۱. فرکانس خط یا شبکه
این فرکانس همان فرکانس موجود در شبکه برق شهری (مانند ۵۰ یا ۶۰ هرتز) است. استفاده از این فرکانس، ارزانترین راه برای راهاندازی یک کوره القایی بدون هسته است، زیرا نیازی به مبدل فرکانس نیست. بار کوره در این حالت معمولاً تکفاز است و تنها یک ترانسفورماتور مورد نیاز است.
در این حالت، میزان بار کوره توسط مسئولین برق شهر تعیین میشود، اگرچه بسیاری از آنها خواستار تعادل نسبی بار، به ویژه در مورد کورههای بزرگ، هستند.
۲. کوره القایی با فرکانس پایین
در این نوع کورهها، ترانسفورماتورهایی که هستههای آنها به حد اشباع مغناطیسی رسیدهاند، جریان متغیری تولید میکنند که شامل نوسانات زیادی است. با اتصال سیمپیچ اولیه به شبکه ستارهای و سیمپیچ ثانویه به مثلث باز، نوساناتی که مضربی از سه هستند میتوانند در مدار ثانویه وجود داشته باشند. این کورهها با ۳ یا ۹ برابر فرکانس شبکه کار میکنند. برای جلوگیری از بازگشت نوسانات به شبکه برق، یک صافی در سیمپیچ اولیه تعبیه میشود. این صافی شامل خازنهایی با فرکانس شبکه است که به صورت موازی به مدار اولیه وصل میشوند. سیمپیچهای بستهای که به صورت سری با سیمپیچهای اولیه قرار گرفتهاند، این صافی را تقویت میکنند. این کورهها نیازی به تنظیم بار ندارند، زیرا بار به محض ورود به طور مساوی بین سه فاز تقسیم میشود. به دلیل کاهش فرکانسها در این حالت، توان ورودی با فرکانسی قویتر از فرکانس شبکه تولید میشود.
۳. کوره القایی با فرکانس بالا
فرکانسهای ۵۰۰ هرتز و بالاتر، کورههای القایی را در دسته فرکانس متوسط قرار میدهند، اما در فرکانس ۲۵۰۰ هرتز از اصطلاح “فرکانس زیاد” استفاده میشود. منبع تغذیه این کورهها معمولاً یک آلترناتور با موتور چند قطبی است.
علاوه بر این، از تعدادی مبدل جرقهای تنظیمکننده یا سوپاپ نیز استفاده میشود. استفاده از مبدلهای فرکانس ثابت که با تریستور کار میکنند، یک نوآوری جدید محسوب میشود. در هر حال، برق از یک منبع سهفاز تأمین میشود. برق ورودی به کوره توسط میدان کنترل شده و به آلترناتور هدایت میشود. به طور کلی، تأمین و نگهداری این تاسیسات بسیار پرهزینه است. فرکانس جریان متناوب عموماً با کاهش توان و اندازه کوره افزایش پیدا میکند.
مزایای مبدلهای ثابت نسبت به موتور ژنراتورها این است که در آنها قسمتهای متحرک وجود ندارد، تنظیم کردن آنها راحتتر است و نیازی به تغییر مداوم ظرفیت دستگاه برای ثابت نگه داشتن ضریب توان برق نیست.
سیستم خنککننده آب
برای محافظت از سیمپیچها و عایق کوره القایی در برابر حرارت شدید، آنها با حجم قابل توجهی آب سرد میشوند. از نظر اقتصادی، بهتر است این آب از رودخانه یا چاه تامین شود. گاهی اوقات آب تصفیه میشود تا از رسوب در داخل لولهها و در نتیجه کاهش جریان آب جلوگیری شود که این امر سرعت خنککنندگی را افزایش داده و عمر کوره را نیز بالا میبرد. همچنین، pH آب در حدود ۸ نگهداری شده و سختی آب گرفته میشود. در برخی موارد، برای کاهش حداکثری خوردگی و گرفتگی، از آب مقطر یا غیر یونیزه در یک مدار بسته استفاده میشود.
پمپها آب را با فشار به داخل سیمپیچ و خازنها هدایت میکنند. اگر آب در کورهها جریان پیدا نکند، کوره قابل راهاندازی نیست؛ زیرا یک کلید فشاری در مدار در نظر گرفته شده است. همچنین، یک مخزن اصلی در محل وجود دارد تا در صورت لزوم، مقادیر آب تحت اثر جاذبه به سمت سیمپیچها جریان یافته و آنها را خنک کند. پس از مصرف، آب از مدار خارج شده و به فاضلاب ریخته میشود، یا در صورت امکان، پس از خنکسازی مجدداً مورد استفاده قرار میگیرد. خنک کردن آب در مسیر جکهایی که آب از بالا به پایین جریان دارد صورت میگیرد. اتلاف آب در مدارهای باز بین ۱۰-۲۰ درصد و در مدارهای بسته کمتر از یک درصد است. در مسیر مدار جریان آب و سیمپیچها، برای جلوگیری از آسیب حرارتی، از کلیدهای مخصوص استفاده میشود.
سیستم ایمنی “اتصال به زمین”
ضخامت آستر در بدنه کورههای القایی با فرکانس زیاد و ظرفیتهای مختلف (مثلاً ۲۵۰ کیلوگرم و ۵۰۰ کیلوگرم) به ترتیب ۳۸ میلیمتر (۱.۵ اینچ) و ۷۵ میلیمتر (۳ اینچ) است که نشاندهنده آسیبپذیری سیمپیچ در برابر نفوذ فلز است. در صورت خرابی آستر، یک سیستم “اتصال به زمین” خطر را به صورت بصری نشان داده و جریان برق را به صورت خودکار قطع میکند. در این سیستم، دستهای سیم به صورت ستارهای، بار را پیوسته به زمین متصل میکند. در مدار، یک میلیآمپرسنج وجود دارد که هنگام عبور جریان از آستر نازک شده، شدت جریان کمتری را نشان میدهد؛ این عمل نشاندهنده اولین اعلام خطر است.
روش دیگر برای اندازهگیری میزان ساییدگی آستر کوره، فقط به هنگام خالی بودن بوته عملی است. اما روش “اتصال به زمین” این خاصیت را دارد که به طور دائم وضعیت آستر را کنترل میکند.
انتخاب فرکانس مناسب
برای کورههای القایی تجاری، فرکانسهای استاندارد شده زیادی وجود دارد که هر یک متناسب با یک کوره خاص و در اندازه و توان معین در نظر گرفته شدهاند. مهمترین عوامل موثر در انتخاب فرکانس عبارتند از:
۱. عمق نفوذ
جریان القایی فقط در لایه سطحی بار (و در اطراف سیمپیچ) ایجاد میشود. عمق نفوذ آن از رابطه زیر محاسبه میشود:
که در آن:
-
= عمق نفوذ
-
= ضریب ثابت
-
= مقاومت مخصوص
-
= قابلیت نفوذ مغناطیسی
-
= فرکانس
از رابطه فوق مشاهده میشود که با افزایش فرکانس، عمق نفوذ کاهش پیدا میکند.
این رابطه برای مواد غیرمغناطیسی، از جمله فولاد در دمای بالاتر از نقطه کوری (دمایی که فولاد خاصیت مغناطیسی خود را از دست میدهد) صادق است.
۲. ظرفیت کوره
جریان القایی از سیمپیچ به داخل کوره نفوذ میکند. عمق نفوذ نباید زیاد باشد، زیرا بافت تداخل این جریان با جریان القایی طرف دیگر سیمپیچ میشود. از آنجا که جریانهای القایی در دو طرف مخالف یکدیگرند، همدیگر را حذف میکنند که موجب کاهش حرارت تولیدی میشود. قطر بار باید حداقل چهار برابر عمق نفوذ باشد. برای بهرهبرداری مفید از برق، ارتفاع سیمپیچ معمولاً بین ۰.۸ تا ۱.۲ برابر قطر آن است. هرچه گنجایش بوته کمتر باشد، فرکانس بالاتری مورد نیاز است.
۳. نوع محصول
در هنگام کار با کورههای القایی با فرکانس شبکه، معمولاً بین یکسوم تا دو-سوم مذاب در کوره نگهداری میشود. عمل ذوب در کورههایی که با فرکانس کم کار میکنند و سرد هستند، با به کارگیری قطعات بزرگ و برگشتیهای کارگاه بهتر شروع میشود. در صورتی که کورههای متوسط با بارکردن قطعات کوچک راحتتر آغاز میشوند.
کورههای القایی با فرکانس شبکه برای تولید فولادهای آلیاژی با ترکیبات مختلف مشکلاتی ایجاد میکنند؛ زیرا تنها با تعویض کامل بار میتوان ترکیبات متنوع و گستردهای را به وجود آورد. برای این کار، استفاده از کوره با فرکانس کم یا متوسط نیاز است. باید توجه داشت که اکسید منیزیم موجود در مواد آسترکشی، میتواند برخی از عناصر نسوز را جذب آلیاژ کند. همچنین، نوع قراضه مصرفی نیز در انتخاب فرکانس موثر است.
۴. توان ورودی
به علت همزدن بار در کوره، توان ورودی حداکثری دارد. با کاهش فرکانس، میزان تلاطم کوره بالا میرود. از این رو، توان ورودی کم است. سرعت ذوب از طریق توان ورودی مشخص میشود. در تاسیسات جدید، رابطه بین فرکانس، ظرفیت و سرعت ذوب در کوره اهمیت ویژهای دارد.
مقایسه مشخصات کورههای القایی بدون هسته
کورههای القایی بدون هسته، بر اساس فرکانس کاری، ویژگیهای متفاوتی از خود نشان میدهند که در انتخاب نوع کوره برای کاربردهای خاص اهمیت زیادی دارد. در ادامه، مقایسهای جامع بین کورههای با فرکانس خط، فرکانس کم و فرکانسهای متوسط و زیاد ارائه شده است.
ویژگی |
فرکانسهای متوسط و زیاد |
فرکانس کم |
فرکانس خطوط اصلی |
راندمان تبدیل |
تقریباً ۸۰% برای آلترناتورها و ۹۰% برای مبدلهای ثابت |
تقریباً ۹۰% |
تقریباً ۹۰% |
اتلاف نیرو بین ذوبها |
دارد (آلترناتور در حال کار است، حتی با باز بودن کنتاکتور اصلی) |
ندارد |
ندارد |
نسبت توان به وزن |
بیشتر از کورههای ۵۰ و ۱۵۰ هرتز؛ مثال: ۹۵۰ کیلووات برای کوره ۲ تنی در ۲۵۰۰ هرتز |
بهتر از کورههای ۵۰ هرتز؛ مثال: ۱۱۰۰ کیلووات برای کوره ۲ تنی |
کم است (به دلیل تلاطم زیاد)؛ مثال: ۸۵۰ کیلووات برای کوره ۲ تنی |
شروع کار از حالت سرد |
ذوب قراضههای کوچک از حالت سرد بدون اشکال انجام میشود؛ امکان ذوب پیدرپی ترکیبات گوناگون |
کار با قراضههای بزرگ و مناسب (مانند تغذیههای سنگین و شمش) شروع میشود. |
مقداری فلز مذاب یا پسماند قبل از شروع کار باید در کوره موجود باشد. |
گرفتن بار کامل |
بار کامل در حین ذوب گرفته میشود. |
وقتی کوره با قراضه بزرگ پر شده و بتوان آن را متعاقباً با قراضههای بزرگ تغذیه کرد (بهویژه قراضه مغناطیسی)، میتوان بار کامل گرفت. اگر کار با قراضههای بزرگ شروع شده و سپس با قراضههای کوچک ادامه یابد، گرفتن بار محدود است تا زمانی که نصف کوره پر شود. |
گرفتن بار کامل، وقتی فقط نیمی یا دو سوم ظرفیت کوره پر شده باشد، نیاز به در نظر گرفتن نوع قراضه مصرفی دارد. |
عمل هم زدن مذاب |
خوب (شدید در مقایسه با ۵۰ هرتز، به دلیل نسبت توان به وزن بالا) |
خیلی شدید |
شدید |
استفاده از آسترهای بازی |
رضایتبخش |
اشکال کمتری نسبت به کورههای ۵۰ هرتز در انگلستان مشاهده شده است. |
مشکلاتی در انگلستان تجربه شده است. |
حداقل توان |
۵۰ کیلووات |
۵۰۰ کیلووات (در کورههای ۱۵۰ هرتز تا ۳۵۰ کیلووات پیشنهاد میشود) |
۳۵۰ کیلووات |
قراضههای ذوب |
میتوان قراضههای مرطوب را ذوب کرد. |
قراضه باید خشک باشد. |
قراضه باید خشک باشد. |
بارگیری و عمل ذوب |
خطراتی پیش نمیآید. |
مانند کوره ۵۰ هرتز میباشد. |
بارگیری میتواند مشکل شود، بهویژه هنگام بارگیری قطعات بزرگ، که باید برق قطع شود. این عمل موجب کاهش بازدهی در حین ذوب قراضههای بزرگ میشود. |
مواد دیرگداز در کوره القایی
کورههای القایی با آسترهای اسیدی، بازی یا خنثی پوشانده میشوند. این آسترها از آجر، بوتههای از پیش شکل داده شده یا مواد دیرگداز مونولیتیک (یکپارچه) ساخته میشوند. کیفیت مواد دیرگداز بسیار مهم است، زیرا تراکم و زینتر شدن مواد را کنترل میکند. با دانهبندی استاندارد (۶۰% مواد درشت، ۱۵% متوسط، ۲۵% ذرات ریز)، حداکثر تراکم به دست میآید. به این ترتیب، ذرات زودتر زینتر شده و بهتر به هم میچسبند. اتلاف حرارت به صورت هدایت در مواد دیرگداز اسیدی کمتر است که این به خاطر قابلیت هدایت حرارتی آنهاست.
-
اکسید منیزیم (): که به آن منیزیت نیز گفته میشود، متداولترین ماده برای پوشش کورههای القایی با آستر بازی است. عیب این آسترها این است که در حین ذوب آلوده میشوند. از دیگر مواد بازی مصرف شده در آسترها میتوان به اکسید آلومینیوم و کروم منیزیت اشاره کرد.
-
کرومیت: که اسپینلی از و است، نیز در کوره استفاده میشود. اما اکسید کروم در فعل و انفعالات احیا میشود و کروم آزاد شده، آستر کوره را به شدت فرسوده میکند. زیرکن نیز در کوره مورد استفاده قرار میگیرد، اما عملکرد آن رضایتبخش نیست، زیرا قابلیت چسبندگی خوبی ندارد و در مقابل اکسید آهن به خوبی اکسید منیزیم نیست.
-
کوارتز: متداولترین مادهای که به عنوان آسترهای اسیدی استفاده میشود، کوارتز است که به صورت سنگهای سیلیسی یافت میشود. سیلیس خالص به محض مواجهه با حرارت منبسط میشود که باعث پر شدن ترکها و محفظههایی میشود که در اثر پایین آمدن دما به وجود آمدهاند.
آسترکشی کورههای القایی
بوتههای کورههای القایی نیز از موادی مشابه خاک نسوز یا سرب سیاه (مخلوطی از خاک رس و گرافیت) ساخته میشوند. این مواد توسط هوا خشک شده و به صورت متراکم و همراه با مواد دانهای خشک بر روی سیمپیچ قرار میگیرند. در ریختهگری، از بوتههای آزاد برای ذوب فلزات غیرآهنی استفاده میشود.
آسترکشی با شکل دادن کف کوره آغاز میشود. در این حالت، حدود دو یا سه اینچ از مخلوط را روی کف کوره ریخته و با ابزاری مناسب میکوبند. سپس شابلون را داخل کوره قرار داده و فضای بین آن که ضخامت آستر است، با چند تکه چوب ثابت میشود. سپس، ریختن و کوبیدن مواد نسوز ادامه مییابد. توجه به این نکته ضروری است که بازرسی سیمپیچ و ترمیم نقاط فرسوده یا نقاطی که بر اثر کندن آستر ناقص شدهاند، عواملی برای افزایش عمر آستر محسوب میشوند. برای ترمیم سیمپیچها از اره، رزین اپوکسی و خمیر آرایست استفاده میشود. الکترومارکت تاکید دارد که نگهداری صحیح از آستر کوره، یکی از مهمترین عوامل در بهرهبرداری بهینه و کاهش هزینههای تعمیر و نگهداری کوره القایی است.
مواد بار (شارژ)
کوره القایی معمولاً به عنوان واحد ذوب اصلی در نظر گرفته میشود. کنترل دقیق واحد شارژ ضروری است تا درصد عناصر آلیاژی تحت تأثیر عوامل و ترکیب هر یک از قطعات قراضه دقیقاً کنترل شود. برای شناسایی نوع آلیاژ، راههایی وجود دارد، از جمله تشخیص رنگ یا چسباندن منبع سردار بر روی سطح قطعه. از آنجا که ممکن است رنگ در عملیات حرارتی یا سایر عملیات پاک شود، بهترین روش علامتگذاری همان استفاده از میخ است.
بار کورههای بازی را معمولاً با ساچمهزنی پاک میکنند تا ماسه موجود در آن از بین برود؛ باقیمانده ماسه باعث میشود که سرباره تولید شده به آستر صدمه بزند. در کورههای اسیدی، ماسه موجود در بار با اکسید آهن ترکیب شده و آستر کمتر آسیب میبیند. معمولاً قبل از بارریزی، روغن اضافه را از روی تراشههای بار میزدایند تا از پاشش بار، تولید دود سیاه و غلیظ و جذب گوگرد در کوره جلوگیری شود. این حالت بیشتر در کورههایی که با فرکانس کم کار میکنند مشاهده میشود.
بار اولیه کوره القایی که با فرکانس کم کار میکند، باید از مواد بزرگ مربع شکل (۱۰۰ تا ۲۰۰ میلیمتر یا ۴ تا ۸ اینچ) تشکیل شده باشد. بهترین پایه برای ذوب در کورههای القایی، مواد از پیش احیا شده هستند، چرا که مواد ناخواسته آنها کم است و این باعث کاهش حجم سرباره میشود. تراکم این مواد کم است و این باعث محدودیتهایی چون مقدار بار و توان ذوب میشود. قراضههای پرآلیاژی به مقدار زیاد برای شارژ این کورهها استفاده میشوند، زیرا اتلاف عناصر آلیاژی بسیار ناچیز است. در کورههایی که با آستر از جنس اکسید منیزیم روکش شدهاند، ذوب یک فولاد کربنی یا فولاد آلیاژی پس از یک فولاد آلیاژی دیگر، باعث جذب مقداری از فولاد آلیاژی قبلی از آستر کوره میشود.
عمل ذوب
در فرآیند ذوب، تنها قراضه به همراه دیگر عناصر آلیاژی غیرقابل اکسید شدن در کوره بارگیری میشوند. موادی که اکسید میشوند، پس از ذوب به کوره اضافه میشوند. مواد پس از بالا رفتن دمایشان تا فوق گداز، سریعاً از کوره خارج میشوند. افزایش دما در کوره با سرعت منظمی بالا میرود که این سرعت به توان کوره بستگی دارد. اکسیژنگیری نهایی در داخل کوره، پاتیل یا هر دو انجام میگیرد. مقدار گاز در فولاد مذاب به سرعت افزایش مییابد. جذب اکسیژن و هیدروژن در دماهای بالاتر بیشتر است. نیتروژن در این گونه موارد حالت استثنایی دارد؛ به این ترتیب که مقدار جذب نیتروژن در دماهای پایین زیاد و در دماهای بالا عملاً صفر است.
در کورههای القایی با فرکانس پایین یا برق شبکه، امکان جذب گاز در هر بارریزی به شدت وجود دارد، مگر اینکه حتیالامکان دمای کوره پایین نگه داشته شود. کوره القایی را نمیتوان یک واحد ذوب کامل در نظر گرفت. فسفر در کورههایی که آستر آنها بازی است، بهتر آزاد میشود. در هنگام جوشش سنگ معدن، گازهای محلول را همانند ذوب در کورههای دیگر از مذاب خارج میکنند. با استفاده از این روش، مقداری هیدروژن و نیتروژن جذب شده کمتر از مقداری است که از عمل ذوب کامل به دست میآید.
چگونگی انتشار گازها در تخلیه کوره
مقاومت فولاد که از راه جوشش سنگ معدن حاصل میشود، بالاتر است. با استفاده از روش جوشش سنگ معدن، مقداری از کربن و دیگر عناصر اکسید شونده از بین میروند. این اتلاف را در وزن بار و مواد افزودنی در نظر میگیریم. استفاده از جوشش سنگ معدن به دلیل بالا رفتن زمان، هزینهبر میشود. عملاً موقعی که نصف کوره از بار پر میگردد، عمل گوگردزدایی شروع میشود. سرباره دارای آهک است که با فلوراسپار روان میشود. چون تلاطم سرباره زیاد است، حوضچه مذاب نیز متلاطم میگردد. در این حالت، فلز و سرباره با یکدیگر مخلوط میشوند.
راندمان کوره القایی
در سیستم الکتریکی کلیه کورههای ذوب برقی، مقدار اتلاف انرژی مشاهده میشود. در این میان، کورههای القایی که با برق شبکه کار میکنند، چون تنها به یک ترانسفورماتور اتصال دارند، کمترین افت را نشان میدهند. در کورههایی که با فرکانس کم کار میکنند، به دلیل تبدیل و تنظیم فرکانس با کمک ترانسفورماتور، میزان افت بیشتر است. کورههای القایی که با فرکانس زیاد و متوسط کار میکنند، به علت داشتن موتور، متناوبساز و ترانسفورماتور در مدار، از افت زیادی برخوردارند.
مقایسه توان لازم برای ذوب چدن تا ۱۶۵۰ درجه سانتیگراد در کورههای القایی بدون هسته (با فرکانسهای مختلف)
توان ذوب (تن بر ساعت) |
مصرف برق (کیلووات ساعت بر تن) ۱۱۰۰ هرتز |
مصرف برق (کیلووات ساعت بر تن) ۱۵۰ هرتز |
مصرف برق (کیلووات ساعت بر تن) ۵۰ هرتز |
۰.۴۵ |
– |
۱۱۰۰ |
۸۵۰ |
۰.۵۰ |
۱۰۰۰ |
۱۰۰۰ |
۱۰۰۰ |
۰.۷۵ |
۹۵۰ |
۹۵۰ |
۹۵۰ |
۱.۰۰ |
۹۰۰ |
۹۵۰ |
۹۵۰ |
۱.۲۵ |
۹۰۰ |
۹۵۰ |
۱۰۰۰ |
۱.۵۰ |
۹۰۰ |
۸۵۰ |
۹۳۰ |
پیشرفتهای جدید در تکنولوژی کوره القایی
کاربرد کورههای تحت فولاد برای کارهای عمومی ریختهگری، در گذشته طرحی عملی نبود. اما در کورههای القایی جدید، درپوشهای متحرکی وجود دارد که در حین ذوب یا بعد از آن به کوره جفت میشوند. با این عمل، مقدار گاز کوره تخلیه شده و گاز کمتری در کوره جمع میشود.
پیشگرم کردن بار کوره قبل از ذوب یا هنگام ذوب، به وسیله یک مشعل سوخت-اکسیژن، باعث بالا رفتن توان ذوب با صرف هزینه کمتر میشود. علاوه بر این، با پیشگرم کردن، موادی که دمای ذوب کمتری دارند و باعث آلودگی مذاب میشوند، قبل از قرار گرفتن بار در کوره ذوب شده و جدا میشوند. این قابلیتها به بهرهوری بیشتر و تولید مذاب با کیفیتتر کمک میکنند. برای مشاوره در زمینه بهینهسازی فرآیندهای ذوب و استفاده از تکنولوژیهای نوین، میتوانید با کارشناسان الکترومارکت در تماس باشید.
مزایای کوره القایی
هزینه خرید و نصب کورههای القایی معمولاً از کورههای قوسی کمتر است. میتوان برای کارهای مختلف از کورههای القایی کوچک در اندازههای متفاوت استفاده کرد. شرایط غیر اکسیدی در کوره القایی منجر به تولید آلیاژهای تثبیت شده میشود. ضمناً، عمل همزدن نیز به یکنواختی فلز در حوضچه مذاب کمک شایانی میکند.
معرفی کوره القایی و سیر تحول آن
کورههای ذوب القایی در ظرفیتهای مختلف (مثلاً از ۱۰۰ کیلوگرم تا ۱۰۰۰ کیلوگرم و بالاتر) موجود هستند و به دلیل وجود بخش کنترل کامل الکترونیک، اپراتوری بسیار سادهای دارند.
مزایای اصلی کوره القایی شامل موارد زیر است:
-
عدم آلودگی و اکسیداسیون بار به علت عدم وجود گاز و شعله اکسیدکننده
-
شروع به کار سریع و عدم نیاز به پیشگرم یا ذوب اولیه
-
سرعت بالای انجام عملیات در مقایسه با سایر کورهها
-
راندمان بسیار بالاتر نسبت به کورههای سوختی
-
قابلیت تهیه آلیاژهای یکنواخت به علت چرخش داخل مذاب
-
قابلیت تهیه و نگهداری ذوب در ظرفیتهای مختلف
-
سادگی عمل تغذیه و تخلیه
-
امکان کنترل دقیق درجه حرارت
-
قابلیت ذوب قراضه
-
اشغال فضای کمتر نسبت به سایر کورهها
-
عدم تأثیر بر آلودگی محیط زیست
تکنولوژی کوره القایی یک تکنولوژی استراتژیک و پرکاربرد است که از جمله در ذوب فلزات با استفاده از انرژی الکتریکی کاربرد دارد. زیربنای صنایع سنگین هر کشور، صنایع ذوب فلزات است و زیربنای صنایع ذوب نیز صنایع کورهسازی است، لذا از اینجا اهمیت صنایع کورهسازی به وضوح روشن میگردد.
در گذشته، بیشتر از کورههای سوخت فسیلی برای ذوب فلزات استفاده میشد. آلودگی محیط زیست، راندمان پایین، سروصدای زیاد، عدم یکنواختی مذاب، عدم توانایی ذوب فلزات دیرگداز و مسائلی از این قبیل، مشکلاتی بود که این کورهها به همراه داشتند.
در چند دهه اخیر، توجه متخصصین و دستاندرکاران کورهسازی به استفاده از انرژی الکتریکی در این زمینه جلب شد و نسل جدیدی از کورههای الکتریکی به وجود آمد که از این میان میتوان به دو مدل از کورههای ذوب اشاره نمود:
-
کورههای قوس الکتریک
-
کورههای القایی
کورههای قوس الکتریک برای ذوب فولاد و به منظور فولادسازی مورد استفاده قرار میگیرند. اما درباره کورههای القایی یا به عبارتی تکنولوژی گرمایش القایی، زمینه بحث بسیار گسترده و عمیق است.
تکنولوژی گرمایش القایی در واقع تولید حرارت توسط میدان متغیر مغناطیسی قوی است که توسط سیستمهای مختلفی قابل تولید است. در گذشته این میدانها را توسط ژنراتورهای دینامیکی تولید میکردند؛ بدین شکل که یک ژنراتور فرکانس متوسط را با یک موتور سهفاز کوپل میکردند و با اضافه کردن یک سری خازن در مدار رزونانس، جریانهای متغیری را در داخل کویل گرمکن به وجود میآوردند. بر این مبنا حرارت در قطعه قرار داده شده در کویل به وجود میآمد.
با پیشرفت تکنولوژی “الکترونیک قدرت” و ساخته شدن سوئیچهای سریع و قوی، نسل جدیدی از ژنراتورها به وجود آمد که اصطلاحاً به آنها ژنراتورهای استاتیکی گفته میشود. در این نوع ژنراتورها حرکت مکانیکی وجود ندارد. به اضافه اینکه کنترل قدرت ژنراتور بسیار دقیقتر و کاملتر میسر است.
نکته مهم دیگر این است که ساخت کوره القایی یک کار تکنولوژیبر است. حداکثر ۲۰ تا ۳۰ درصد قیمت یک کوره، مواد به کار رفته در آن میباشد و بقیه قیمت، تکنولوژی آن است. به همین دلیل است که تکنولوژی آن را به ما نمیفروشند.
اهمیت این تکنولوژی در این مطلب نهفته است که زیربنای بسیاری از تکنولوژیها و صنایع میباشد و به عبارتی اکثر صنایع سنگین به نوعی به این تکنولوژی وابسته هستند. مطلب دوم اینکه این تکنولوژی خود بسترساز بسیاری از تکنولوژیهای دیگر است که به نوبه خود برای کشور مفید خواهند بود. با توجه به نیاز کشور به این تکنولوژی، به نظر میرسد باید نظر مسئولین مربوطه نسبت به این صنعت بیشتر جلب گردد تا در آینده بتوانیم شاهد شکوفایی و رشد و ترقی روزافزون این تکنولوژی در کشور باشیم.
مزایای کورههای القایی نسبت به سایر کورهها (تکراری برای تاکید)
-
اپراتوری بسیار ساده به علت وجود بخش کنترل کامل الکترونیک
-
عدم آلودگی و اکسیداسیون بار به علت عدم وجود گاز و شعله اکسیدکننده
-
شروع به کار سریع و عدم نیاز به پیشگرم یا ذوب اولیه
-
سرعت بالای انجام عملیات در مقایسه با سایر کورهها
-
راندمان بسیار بالاتر نسبت به کورههای سوختی
-
قابلیت تهیه آلیاژهای یکنواخت به علت چرخش داخل مذاب
-
قابلیت تهیه و نگهداری ذوب در ظرفیتهای مختلف
-
سادگی عمل تغذیه و تخلیه
-
امکان کنترل دقیق درجه حرارت
-
قابلیت ذوب قراضه
-
اشغال فضای کمتر نسبت به سایر کورهها
-
عدم تأثیر بر آلودگی محیط زیست
کورههای القایی در مقایسه با کورههای سوخت فسیلی دارای مزایای فراوانی از جمله دقت بیشتر، تمیزی و تلفات گرمایی کمتر و … هستند. همچنین در کورههایی که در آنها از روشهای دیگر، غیر القا استفاده میشود، اندازه کوره بسیار بزرگ بوده و زمان راهاندازی و خاموش کردن آنها طولانی است.
عبور جریان از یک سیمپیچ و استفاده از میدان مغناطیسی برای ایجاد جریان در هسته سیمپیچ، اساس کار کورههای القایی را تشکیل میدهد. در این کورهها از حرارت ایجاد شده توسط تلفات فوکو و هیسترزیس برای ذوب فلزات یا هرگونه عملیات حرارتی استفاده میشود.
نخستین کوره القایی که مورد بهرهبرداری قرار گرفت، از شبکه اصلی قدرت تغذیه میشد و هیچگونه تبدیل فرکانسی صورت نمیگرفت. با توجه به اینکه افزایش فرکانس تغذیه کوره موجب کاهش ابعاد آن و بالا رفتن توان (تلفات) میشود، برای رسیدن به این هدف، در ابتدا منابع تغذیه موتور ژنراتوری مورد استفاده قرار گرفت.
هرچند با این منابع میتوان فرکانس را تا حدودی بالا برد، ولی محدودیت فرکانس و عدم قابلیت تغییر آن و در نهایت عدم تطبیق سیستم تغذیه با کوره، دو عیب اساسی این سیستمها به شمار میرفت. با توجه به این معایب، ورود عناصر نیمههادی به حیطه صنعت موجب گردید منابع تغذیه استاتیک جایگزین منابع قبلی شوند.
در سال ۱۸۳۱ میلادی، مایکل فارادی با ارائه این مطلب که اگر از سیمپیچ اولیهای جریان متغیری عبور کند، در سیمپیچ ثانویه مجاورش نیز جریان القا میشود، تئوری گرمایش القایی را بنا نهاد. علت اصلی این پدیده القا، تغییرات شار در مدار بسته ثانویه است که از جریان متناوب اولیه ناشی میشود.
نزدیک به یکصد سال این اصل در موتورها، ژنراتورها، ترانسفورماتورها، وسایل ارتباط رادیویی و … به کار گرفته میشد و هر اثر گرمایی در مدارهای مغناطیسی به عنوان یک عنصر نامطلوب شناخته میشد.
در راستای مقابله با اثرات حرارتی در مدارهای مغناطیسی و الکتریکی، از سوی مهندسین گامهای موثری برداشته شد. آنها توانستند با مورق نمودن هسته مغناطیسی موتورها و ترانسفورماتورها، جریان فوکو (Eddy Current) را که عامل تلفات حرارتی بود، مینیمم نمایند.
به دنبال آزمایشات فارادی، قوانین متعددی پیشنهاد شد. قوانین لنز و نیومن نشان دادند که جریان القا شده با شار القایی مخالفت کرده و به طور مستقیم با فرکانس متناسب میباشد. فوکو در سال ۱۸۵۵ در مقالهای تحت عنوان “القا جریان در هسته” که توسط هویساید منتشر گردید، نظریهای راجع به جریان فوکو ارائه داد و در رابطه با انتقال انرژی از یک کویل به یک هسته توپر بحث نمود. علاوه بر افراد فوق، تامسون نیز در ارائه نظریه گرمایش از طریق القا سهم بسزایی داشت.
در اواخر قرن نوزدهم، استفاده از تلفات فوکو و هیسترزیس به عنوان منبع گرمایش القایی از طرف مهندسین مطرح شد. همچنین در اوایل قرن اخیر در کشورهای فرانسه، سوئد و ایتالیا بر اساس استفاده از خازنهای جبرانکننده توان راکتیو، پیشنهاداتی برای کورههای القایی بدون هسته ارائه شد. در این پیشنهادات بیشتر ذوب فلزات در فرکانسهای میانی مورد نظر بود.
دکتر نورثروپ ایده کوره با فرکانس میانی را برای موارد صنعتی گسترش داد. در روزهای نخستین، بر اثر نبود امکانات از جمله خازنهای با ظرفیت کافی و قابل اطمینان، توسعه و پیشرفت متوقف شد. بعدها در سال ۱۹۱۶ کمپانی کورههای الکتریکی (EFCO) نخستین کوره القایی با فرکانس میانی را در شفیلد انگلستان و به منظور آهنگری و گرمادهی موضعی فلزات جهت اتصال به یکدیگر، نصب کرد.
بعد از این، تعداد و اندازه این کورهها رو به افزایش گذاشته است. لازم به ذکر است که مزیتهای دیگر کورههای القایی همچون دقت زیاد برای گرم کردن تا عمق مورد نظر و حرارت دادن نواحی سطحی در طی پیشرفتهای بعدی (در سالهای جنگ جهانی دوم) بیشتر آشکار شد. در گرمایش القایی، عدم نیاز به منبع خارجی گرمکننده، تلفات گرمایی کمتر شده و تمیزی شرایط کار تامین میگردد. در این روش همچنین نیازی به تماس فیزیکی بار و کویل نبوده و علاوه بر این چگالی توان بالا در مدت زمان گرمایش کم به آسانی قابل دسترس میباشد.
در ابتدا کورههای القایی مستقیماً از شبکه قدرت تغذیه میشدند که به نوبه خود گام موفقی در استفاده از توان الکتریکی جهت عملیات حرارتی به حساب میآمد.
از آنجایی که تلفات فوکو و هیسترزیس با فرکانس نسبت مستقیم دارند و اینکه ابعاد کویل کوره با بالا رفتن فرکانس کاهش مییابد، مهندسین به فکر تغذیه کوره در فرکانسهای بالاتر از فرکانس شبکه قدرت افتادند. اولین قدم در این راه استفاده از فرکانسهای دو برابر و سه برابر که از هارمونیکهای دوم و سوم به دست میآمدند، بود.
این هارمونیکها بر خلاف طبیعت مخرب خود در این نوع کاربرد سودمند تشخیص داده شدند. پایین بودن راندمان در استفاده از هارمونیکهای فوق موجب گردید طراحان روش دیگری را مورد استفاده قرار دهند. در این مرحله سیستم موتور-ژنراتور توسعه یافت که با استفاده از این سیستم توانستند فرکانس تغذیه را تا صدها هرتز افزایش دهند. در کورههای القایی، افزایش فرکانس باعث کاهش عمق نفوذ جریان القایی میگردد، لذا در عملیات حرارتی سطحی که سختکاری سطح فلز مورد نظر میباشد، از کورههای القایی با فرکانس بالا استفاده میشود.
دستهبندی سیستمهای القایی بر اساس منبع تغذیه و فرکانس
با ورود عناصر نیمههادی مانند تریستورها، ترانزیستورها و ماسفتها به صنعت، محدودیتهای فرکانس و عدم تغییر آن در تغذیه کورهها برطرف شد. از لحاظ سیستم قدرت، میتوان سیستمهای القایی را به چهار دسته اصلی تقسیم کرد:
الف. سیستمهای منبع (Supply Systems)
در این سیستمها که فرکانس کار آنها بین ۵۰ تا ۱۵۰ هرتز و ۱۰۰۰ تا ۱۰۰۰۰ هرتز است، نیازی به تبدیل فرکانس نیست. با توجه به فرکانس کار، عمق نفوذ جریان زیاد بوده و حدود ۵۰ تا ۵۰۰ میلیمتر است. همچنین مقدار توان لازم میتواند تا چندین صد مگاوات نیز برسد.
ب. سیستمهای موتور-ژنراتور (Motor-Generator Systems)
فرکانس این سیستمها از ۱۵۰ هرتز تا ۱۰ کیلوهرتز است. در این سیستمها تبدیل فرکانس لازم بوده و این عمل بهوسیله ژنراتورهای کوپلشده با موتورهای القایی صورت میپذیرد. همچنین در این سیستمها توان بهوسیله ماشینهای ۵۰۰ کیلووات تأمین میگردد و برای بهدست آوردن توانهای بالاتر، از سری کردن ماشینها استفاده میشود. عمق نفوذ در این سیستمها به خاطر بالاتر بودن فرکانس نسبت به سیستمهای منبع، کمتر بوده و در حدود ۱۰ تا ۵۰ میلیمتر است.
ج. سیستمهای مبدل نیمههادی (Solid-State Converter Systems)
در این سیستمها فرکانس در محدوده ۵۰۰ هرتز تا ۵۰۰ کیلوهرتز بوده و تبدیل فرکانس به روشهای گوناگونی صورت میپذیرد. در این سیستمها از سوئیچهای نیمههادی استفاده میشود و توان مبدل بستگی به نوع کاربرد آن تا حدود ۱ مگاوات میتواند برسد.
د. سیستمهای فرکانس رادیویی (Radio-Frequency Systems)
فرکانس کار در این سیستم در محدوده ۱۵۰ کیلوهرتز تا ۲۰ مگاهرتز است. از این سیستمها برای عمق نفوذ جریان بسیار سطحی، در حدود ۰.۵ تا ۱ میلیمتر استفاده میگردد و در آن از روش گرمایی متمرکز با سرعت تولید بالا بهره گرفته میشود.
کورههای ذوب القایی در فولادسازی
امروزه ذوب القایی به صورت گستردهای در تولید و ریختهگری فولادها و همچنین ذوب آلومینیوم، مس، روی و سایر انواع فلزات غیرآهنی استفاده میشود. از مزایای ذوب القایی میتوان به راندمان بالای مواد و محیط پاک اشاره کرد که باعث تمایل تولیدکنندگان محصولات فلزی به کورههای ذوب القایی شده است.
در کورههای ذوب القایی، جریان الکتریکی القا شده توسط میدان مغناطیسی، ایجاد حرارت میکند و این حرارت باعث ذوب جسم (معمولا فلزات) میشود. فلز درون بوتهای قرار میگیرد که اطراف آن کلافهای مغناطیسی پیچیده شده است و توسط جریان آب خنک میشوند. جریان موجود در کلافهای مغناطیسی، جریانهای گردابی یا فوکو (Eddy Current) را در فلز القا میکند که باعث ایجاد حرارت و ذوب فلز میشود.
مهمترین انواع کورههای القایی، کوره القایی بیهسته (Coreless furnace) و کوره القایی کانالی (Channel Furnace) هستند. در کوره القایی بدون هسته، فلز درون یک پوشش نسوز که بهوسیله کلاف احاطه شده است، نگهداری میشود.
در این حالت، کوره ذوب القایی مشابه یک ترانسفورماتور عمل میکند؛ بدین ترتیب که فلز مانند یک کلاف ثانویه در ترانسفورماتور عمل میکند و با اعمال نیرو به کلاف اولیه احاطهکننده فلز، جریانهای گردابی القا شده و تولید حرارت میکنند.
پس از ذوب فلز، هم زدن و همگنسازی به طور طبیعی و در اثر وجود نیروها و جریانهای الکترومغناطیسی اتفاق میافتد. با انتخاب دقیق فرکانس و نیرو میتوانند سرعت ذوب و همگنسازی را کنترل کرد. کورههای القایی کانالی در گذشته عموماً برای نگهداری فلز مذاب در یک دمای مشخص کاربرد داشتهاند، اما امروزه گاهی اوقات برای ذوب فلزات نیز به کار میروند. این کوره شامل یک القاگر (سلف) به عنوان منبع تولید انرژی است که از چندین رشته کلاف که توسط آب خنک میشوند، تشکیل شده است. این کورهها تلاطم سطحی کمتری در بوته نگهداری فلز مذاب دارند، در نتیجه خروج گاز و مواد فرار با مشکل مواجه میشود.
لذا جهت عملیات ذوب، کوره القایی بیهسته ترجیح داده میشود و کوره کانالی بیشتر به منظور نگهداری فلز مذاب در یک دمای مشخص مورد استفاده قرار میگیرد. در حالی که کورههای ذوب القایی کانالی دارای فرکانس خطی هستند، کورههای بدون هسته میتوانند از هر سه نوع فرکانس خطی (۵۰ هرتز)، فرکانس متوسط (۱۵۰-۱۵۰۰ هرتز) و فرکانس بالا (بیش از ۱۵۰۰ هرتز) باشند. با توجه به اینکه شروع به کار کورههای فرکانس خطی با شارژ ماده سرد بسیار آهسته است، استفاده از کورههای فرکانس متوسط و بالا مورد توجه بیشتری قرار دارد.
استفاده از کورههای ذوب القایی در ظرفیتهای پایینتر از ۱۰ تن میتواند منجر به تولید مذاب با کیفیت مناسب و ارزان شود. از مزایای این نوع کورهها میتوان به اپراتوری و کارکرد آسان و همچنین افزایش راندمان ذوب فلز اشاره کرد. امکان راهاندازی و شروع به کار فوری کوره باعث کاهش در زمان رسیدن به دمای کارکرد میشود. وجود همگنسازی به صورت طبیعی و تولید مذاب پاک و عدم نیاز به سیستمهای کنترل آلودگی با هزینه بالا از مزایای دیگر کورههای القایی محسوب میشود.
از دیگر نکات مثبت این کورهها میتوان به موارد زیر اشاره کرد:
-
عدم نیاز به فضای زیاد و توانایی افزایش سرعت ذوب در کورههای کوچک
-
مصرف کمتر مواد، به خصوص مواد نسوز و کاهش زمان تعویض پوششهای نسوز و عدم نیاز به مصرف
-
الکترود گرافیتی
-
پایین بودن آلودگی صوتی به نسبت انواع دیگر کورههای ذوب به میزان قابل توجه
-
بهرهوری بالای انرژی
-
هزینه پایین سرمایهگذاری و تجهیزات جانبی
از طرف دیگر، مهمترین اشکال کورههای القایی دشواری در فرآیند فسفرزدایی و انجام عملیات متالورژیکی ثانویه است. در نتیجه وجود کورههای پاتیلی (Ladle Furnace) در کنار این کورهها جهت انجام فرآیند تصفیه و افزودن عناصر آلیاژی لازم است.
از دیگر معایب این کورهها، ظرفیت پایینتر تولید به نسبت کورههای قوس الکتریک میباشد. همچنین در کورههای القایی باید از قراضه با کمترین آلودگی و مواد اکسیدی استفاده نمود که گاهی این مسئله دشوار و باعث افزایش هزینههای اولیه میگردد.
همچنین استفاده از آهن اسفنجی به عنوان شارژ کمکی برای تنظیم خواص شیمیایی در این کورهها موجب بهبود عملکرد کورههای ذوب القایی شده است. با استفاده از آهن اسفنجی، میزان کربن مذاب بر اساس مشخصات خواسته شده قابل تنظیم بوده و با توجه به اینکه در آهن اسفنجی عناصر و فلزات مضر وجود ندارد، فلز مذاب به دست آمده تمیز و عاری از عناصر مضر خواهد بود.
قبل از ورود مواد فلزی به کوره، آنالیز شیمیایی این مواد جهت دستیابی به مشخصات نهایی محصول، به دقت کنترل میشود. اگر میزان کربن، گوگرد و فسفر در شارژ فلزی بالا باشد، مقدار بیشتری آهن اسفنجی به کوره شارژ میشود. پس از اتمام ۸۰ درصد ذوب، نمونهای از کوره گرفته میشود و در صورتی که مقدار کربن همچنان بالا باشد، مجدداً نرمه آهن اسفنجی به کوره شارژ میشود.
از طرفی باید در نظر داشت به دلیل اینکه آهن اسفنجی دارای تخلل میباشد و همین عامل باعث مقاومت در عبور جریان میشود، جهت جلوگیری از مصرف بالای برق، حداکثر میتوان ۱۰-۲۰ درصد شارژ فلزی را به آهن اسفنجی اختصاص داد.
تحقیقات جدید و توسعه در تامین نیرو با فرکانسهای متغیر، بهبود در پوششهای نسوز، طراحی القاگر با توان بالا، بازیافت حرارت کوره و استفاده از سیستمهای کامپیوتری و اتوماسیون موجب بهبود راندمان کورههای ذوب القایی و تمایل به استفاده از آنها شدهاند. علاوه بر این، در سالهای اخیر با تکنولوژی کورههای القایی دوقلو که دارای دو بوته هستند، امکان افزایش راندمان و سرعت تولید مذاب فراهم شده است.
فرآیند ذوب القایی روشی است که بهوسیله جریانهای گردابی القا شده توسط میدان الکترومغناطیسی متغیر، در ماده هادی الکتریسیته (معمولا فلزات) حرارت ایجاد نموده و فرآیند ذوب انجام میشود. اساس کار این روش مشابه ترانسفورماتور است.
اجزای مختلف کوره القایی
به طور کلی اجزای مختلف کورههای القایی عبارتند از:
الف: بوته
شامل اسکلت فلزی کوره، کویل (سیمپیچ)، جداره نسوز، هسته ترانسفورماتور، یوغها (yokes) و پلتفرم (سکو).
ب: تاسیسات الکتریکی
شامل دژنکتور، سکسیونر، ترانسفورماتور، مبدل فرکانس، خازنها، چوکها، کلیدهای کولرها، مکندهها و تابلوهای کنترل.
ج: تاسیسات خنککننده
تاسیسات الکتریکی کوره القایی مانند ترانسفورماتور، چوک، خازنها، کلیدهای فشار قوی و تابلوی مدار فرمان در محدوده زمانی خاصی میتوانند کار کنند و اگر از حد معینی گرمتر شوند باعث ایجاد مشکلاتی میگردند، لذا این تاسیسات باید خنک گردند. خنک کردن تاسیسات الکتریکی میتواند با فن، ایرکاندیشن یا کولر گازی صورت گیرد.
کویل و بدنه کوره در کورههای بوتهای و کویل، پوسته اینداکتور، پوسته خنککن و گلویی کوره در کورههای کانالدار نیز باید خنک شوند. این قسمتها عموماً با آب خنک میگردند (برخی از کورههای کوچک کانالدار به گونهای طراحی میشوند که تمام قسمتهای ذکر شده یا قسمتی از آن با هوا خنک میشود) و تاسیسات مخصوصی شامل مبدلهای حرارتی، پمپ، برج خنککن و غیره را دارا میباشند و معمولاً مقصود از تاسیسات خنککن همین قسمت میباشد.
د: تاسیسات حرکت بوته
برای کورههای بزرگ هیدرولیکی و برای کورههای کوچک مکانیکی یا هیدرولیکی است و شامل جکهای هیدرولیک، پمپ هیدرولیک، مخزن روغن، شیرها، دیگر تاسیسات هیدرولیک و میز فرمان هیدرولیک یا سیستمهای چرخدندهای دستی یا چرخدندهای موتوردار.
ه: محل استقرار کوره
شامل اتاق محل استقرار بوته (Pit Furnace)، فونداسیون، چاله تخلیه اضطراری، محل استقرار تاسیسات الکتریکی، هیدرولیکی و خنککن و محل استقرار تابلوهای مدار فرمان، تابلوی کنترل مدار آب و میز فرمان هیدرولیک میباشد.
و: تاسیسات تهویه
تاسیسات دود و غبارگیر، به خصوص در کورههای بوتهای بزرگ را نیز میتوان از تاسیسات مهم به حساب آورد.
تاسیسات کورههای القایی و عوامل موثر بر عملکرد آنها
هر کدام از شش قسمت فوق، مسائل و برنامه تعمیر و نگهداری مخصوص به خود را دارد که این برنامه بسته به نوع کوره (کانالدار، بوتهای)، ظرفیت بوته، فرکانس کوره (خطی، متوسط، بالا)، سیستم خنککن کوره، سیستم حرکت بوته و نوع جداره نسوز تفاوتهایی داشته، اما در اصول همسانی زیادی وجود دارد.
به طور کلی مسائل مربوط به کورههای القایی بوتهای و کانالدار، از جمله عوامل موثر در کار کوره، چگونگی کنترل خوردگی و سایش و … با یکدیگر تفاوتهایی دارند؛ لذا بهتر است در این بررسی هر کدام به صورت جداگانه مورد مطالعه قرار گیرند.
عوامل موثر در کار کورههای القایی
مهمترین عوامل موثر در بالا بودن راندمان کاری کوره عبارتند از: اجرای دقیق برنامه تعمیر و نگهداری کوره، شارژ مناسب، اپراتوری صحیح، وضعیت جداره نسوز.
اجرای دقیق برنامه تعمیر و نگهداری کوره
کورههای القایی بسته به نوع آن (کانالدار، بدون هسته)، ظرفیت آن، مقدار فرکانس، نوع سیستم خنککن، سیستم حرکت بوته و نوع جداره نسوز، برنامه تعمیر و نگهداری مخصوص به خود دارد و باید به دقت اجرا شود. اصول و خطوط کلی تعمیر و نگهداری کوره القایی در قسمتهای بعدی بررسی خواهد شد.
شارژ مناسب
کورههای بدون هسته ذوب القایی با فرکانس پایینتر از ۲۰۰ هرتز، تمام ذوب خود را تخلیه نمیکنند تا زمان شارژ بعدی کوتاهتر شود. به علت وجود ذوب در این کورهها، مواد شارژ باید عاری از روغن و رطوبت باشد، در غیر این صورت خطر پاشش ذوب و قطعات شارژ جامد به بیرون از کوره وجود دارد. ضمناً وجود روغن و دیگر مواد آلی باعث ایجاد دود در کارگاه میشود.
سرد بودن سرباره نسبت به ذوب در کورههای القایی، ضمن اینکه این کورهها را در امر احیای مواد اکسیدی ناتوان میکند، باعث میشود این کورهها نتوانند مقدار زیاد مواد اکسیدی، خاک و سرباره را تحمل کنند و وجود مقادیر زیاد مواد غیرفلزی غیرآلی باعث ایجاد پل بالای ذوب بهخصوص هنگام سرد بودن ذوب میشود که خود میتواند مشکلاتی را در کار کوره ایجاد کند. ابعاد نامناسب شارژ نیز میتواند هم مستقیماً به جداره صدمه بزند و هم در ایجاد پل روی ذوب کمک نماید.
اپراتوری صحیح
چرخش و تلاطم مذاب در کورههای القایی بدون هسته، بهخصوص با فرکانسهای پایینتر، باعث میشود تهیه ذوب با آنالیز معین و همگن و درجه حرارت مشخص و یکنواخت سادهتر باشد.
با این حال، برای بالا رفتن راندمان و سلامت کوره اصولی در کار با کوره باید رعایت کرد. انتخاب شارژ مناسب، دمای صحیح ذوب در مراحل مختلف فرآیند تهیه ذوب، شارژ کوره به روش صحیح و مقادیر معین، توجه به تابلوهای مدار فرمان و ابزار و وسایل هشداردهنده و توجه به مسائل ایمنی از جمله وظایفی است که اپراتور کوره (کورهدار) هنگام کار با کوره باید رعایت کند. اپراتوری کوره با توجه به نوع کوره، ظرفیت آن، نوع ذوب تهیه شده، نوع شارژ جامد و پارامترهای دیگر تفاوت میکند.
برنامه تعمیر و نگهداری کوره، انتخاب شارژ مناسب و اپراتوری صحیح از جمله دستورالعملهایی است که معمولاً فروشنده یا سازنده کوره همراه کوره ارسال میکند و میبایست جهت سلامت و بالا بودن راندمان کوره به آنها عمل کرد.
وضعیت جداره نسوز
جداره کورههای القایی میتواند در اثر سایش مکانیکی به وسیله ذوب و شارژ جامد، خوردگی شیمیایی به وسیله سرباره، ذوب و اتمسفر کوره، شوکهای مکانیکی و حرارتی، کندگی و انهدام در اثر برخورد و تصادم با شارژ جامد، شیوه شارژ نامناسب و غیرمتناسب بودن ابعاد و کیفیت شارژ، درجه حرارت بیش از اندازه بالای ذوب، آسیب دیده یا نازک گردد (نصب و پخت ناصحیح جداره و هرگونه انفجار به هر دلیلی داخل کوره نیز میتواند باعث انهدام یا آسیب به جداره نسوز شود). و یا در اثر رسوب مواد غیرفلزی، غیرآلی بر جداره ضخیم گردد که در هر دو مورد برای کوره مضر میباشد.
مورد اول (نازک شدن جداره)، گرچه در مرحله اول باعث بالا رفتن توان گرمایی کوره میشود، ولی در مجموع عمر جداره را پایین آورده و گاهی باعث توقف اضافی میگردد. مورد دوم (ضخیم شدن جداره)، باعث پایین آمدن راندمان کوره شده و گاهی در شارژ کردن نیز اخلال ایجاد میکند. برای شناخت علل ضخیم شدن جداره و نازک شدن جداره بر اثر فعال و انفعالات شیمیایی باید ترمومتالورژی ذوب، سرباره، اتمسفر کوره و آستر نسوز را شناخت. به عنوان مثال، وجود اکسیدهای قلیایی در ذوب آلومینیوم در کورههای با جداره آلومینایی باعث اکسید شدن آلومینیوم مذاب و تشکیل آلومینا و رسوب آن بر جداره و در نتیجه ضخیم شدن جداره میگردد، در صورتی که وجود اکسیدهای قلیایی در کورههای با جداره سیلیسی باعث خوردگی شدید آستر نسوز میگردد.
کنترل خوردگی و سایش
جداره کورههای بوتهای بسته به شرایط کاری، نوع ذوب، نوع جداره از نظر شیمیایی و فیزیکی، نحوه نصب، رطوبتگیری و پخت آستر، نوع و کیفیت شارژ جامد و نحوه شارژ، میتواند هنگام کار ضخیم گردد یا اینکه در اثر سایش، فرسایش، خوردگی شیمیایی نازک گردد. نازک شدن جداره به مفهوم نزدیک شدن جداره و نزدیک شدن ذوب به کویل است. فوران مغناطیسی جذب شده توسط کویل افزایش پیدا کرده و نتیجتاً آمپری که توسط کویل در یک ولتاژ معین کشیده میشود (با یک حجم ذوب معین و در فرکانس مشخص برای کورههای متغیر)، در حالت جداره نو با حالت جداره خورده شده مقایسه گردد، افزایش آمپر مشاهده خواهد شد. با اضافه شدن مقدار آمپر کشیده شده که بیانگر جذب بیشتر فوران مغناطیسی توسط ذوب است، خاصیت سلفی (Inductive) مدار بیشتر میشود و در نتیجه ضریب توان () از یک به سمت خاصیت سلفی منحرف میشود. برای یک کردن ضریب توان، نیاز به مقدار خازن بیشتری در مدار میباشد. بنابراین، بهترین راه کنترل خوردگی جداره زمانی که ذوب داخل کوره میباشد، مشاهده مقدار جریان الکتریکی کشیدهشده توسط کویل، ضریب توان و مقدار خازنهای داخل مدار و مقایسه آنها با حالت جداره نو میباشد.
عکس مطالب فوق در هنگامی است که جداره ضخیم گردد. بدین معنا که با ضخیم شدن جداره، ذوب از کویل دور شده و در نتیجه حجم فوران مغناطیسی جذب شده توسط ذوب کاهش مییابد و بالطبع جریان کشیده شده توسط کویل کم میشود و در نتیجه مدار خازنی (capacitive) میشود و ضریب توان () از یک به سمت خازنی منحرف میگردد و برای یک کردن نیاز است مقداری خازن از مدار خارج شود. بنابراین با کنترل مداوم آمپر کشیده شده توسط کویل، ضریب توان و مقدار خازن در مدار برای تصحیح ضریب توان و مقایسه آن با حالت جداره نو میتوان دریافت که جداره نازک شده است و یا ضخیم.
مقادیر الکتریکی فوق را میتوان در رابطه زیر خلاصه کرد:
-
: مقاومت حمام مذاب (اهم)
-
: ولتاژ کوره (ولت)
-
: توان کوره (وات)
مقاومت حمام زمانی که از مذاب پر است و درجه حرارت ذوب نزدیک به درجه حرارت استفاده میباشد و ولتاژ کوره در یکی از ولتاژهای بالا قرار دارد، اندازهگیری میشود. این اندازهگیری به طور مداوم از زمانی که کوره نوکوبی شده است، انجام میشود. کاهش مقاومت حمام به معنای نازک شدن جداره و نزدیک شدن ذوب به کویل است و افزایش مقاومت حمام به مفهوم ضخیم شدن جداره و دور شدن ذوب از کویل میباشد. معمولاً اگر مقاومت خام ۱۵ درصد کاهش یافت، به مفهوم این است که جداره نسوز نیاز به تعمیر دارد.
این نکته را باید یادآور ساخت که با نازک یا ضخیم شدن جداره، بالانس فاز کوره هم نامتعادل شده و در نتیجه مقدار خازن در مدار برای متعادل کردن فازها نیز تغییر میکند؛ منتها جهت کنترل خوردگی یا ضخیم شدن جداره نیاز چندانی به کنترل بالانس فاز نمیباشد. از طرفی با خورده شدن جداره یا ضخیم شدن آن، مقدار حرارت منتقل شده به کویل تغییر یافته و در نتیجه گرمای آب عبوری از داخل کویل تفاوت میکند و اختلاف دمای آب ورودی با آب خروجی تغییر میکند. با نزدیک شدن ذوب به کویل، اختلاف دمای ورودی و خروجی افزایش و با دور شدن، کاهش مییابد. اگرچه عوامل مهم دیگری نیز موثر هستند، این پارامتر به تنهایی نمیتواند معیار سنجش قرار گیرد و باید در کنار پارامترهای الکتریکی فوقالاشاره از آن بهره گرفت.
در برخی از کارخانجات این مفهوم اشتباه به وجود آمده است که نزدیک شدن ذوب به کویل را اهممتر کوره نشان میدهد، در صورتی که اهممتر مقاومت الکتریکی جداره را تعیین مینماید و جداره سالم حتی با ضخامتی معادل کمتر از ضخامت اصلی، دارای مقاومت الکتریکی به اندازه کافی بالایی است که اهممتر نتواند تشخیص بدهد. اگر جداره خیس باشد یا در اثر نفوذ ذوب به جداره، اتصال کوتاه به وجود آمده باشد، اهممتر وضعیت را نشان میدهد. زمانی که اهممتر اعلام خطر مینماید (در بعضی کورهها اهممتر مقاومت الکتریکی تمام قسمتهای تاسیسات الکتریکی کوره و بوته را همزمان کنترل میکند، در این حالت باید اول مشخص گردد که اتصال کوتاه در بوته است یا تاسیسات الکتریکی و بعد تصمیمات لازم اتخاذ گردد)، چه از خیس شدن جداره و چه از اتصال کوتاه باشد، باید بلافاصله کوره تخلیه گردد و در جهت رفع عیب تلاش شود. یادآوری این نکته ضروری است که در زمان پخت جداره، مقاومت الکتریکی جداره به خاطر وجود مختصری رطوبت در جداره پایین است که این مورد غیر از موارد یاد شده در فوق میباشد. بنابراین مشخص است که اهممتر خوردگی جداره را نشان نخواهد داد و هنگامی که اهممتر مشخص میکند مقاومت الکتریکی جداره پایین آمده است، به مفهوم اعلام خطر است و باید ذوب کوره بلافاصله تخلیه گردد. پس مقاومت الکتریکی جداره جهت کنترل سلامت جداره باید مرتب و مداوم بازرسی گردد، ولی جهت کنترل نازک یا ضخیم شدن جداره در هنگام پر بودن کوره از ذوب باید از ضریب توان () مدار، آمپر کشیده شده توسط کویل و مقدار خازن تصحیح $ \text{cos}\alpha $ بهره جست. مشخص است در صورتی که خوردگی جداره موضعی باشد یا در ناحیهای خوردگی و در ناحیه دیگر افزایش ضخامت جداره به وجود آمده باشد، نمیتوان از طریق فوقالذکر کنترل دقیقی بر وضعیت جداره داشت، چرا که خوردگی موضعی کوچک، گرچه میتواند خطرآفرین باشد، اما تأثیر چندانی بر آمپر کشیده شده توسط کویل ندارد و در صورتی که خوردگی در یک ناحیه با ضخیم شدن در ناحیه دیگر توأم باشد، به علت خنثی کردن اثر یکدیگر باعث گمراهی کنترلکننده خواهد شد. بنابراین باید جهت کنترل دقیقتر وضعیت جداره از روشهای دیگری هم استفاده کرد.
در کورههای با فرکانس بالاتر از ۱۵۰ هرتز، چون ذوب کوره پس از آماده شدن کاملاً تخلیه میگردد، میتوان از مشاهده مستقیم نیز استفاده کرد و خوردگیهای موضعی را تشخیص داد. در کورههای با فرکانس خط و فرکانس سه برابر (۱۵۰ یا ۱۸۰ هرتز)، چون ذوب کوره کاملاً تخلیه نمیگردد، مشاهده تمام کوره امکان ندارد، اما قسمتهای فوقانی را میتوان مشاهده کرد. تا اینجا باید خاطرنشان ساخت که کنترل مطمئن و کاملتر باید در فواصلی که کوره تخلیه میگردد و جداره سرد میشود (مثل تعطیلات پایان هفته)، ابعاد بوته با دقت اندازهگیری گردد و از مقایسه آن با حالت نو، ضخامت جداره به دست آید. بهترین راه اندازهگیری ضخامت جداره از طریق اندازهگیری شعاع بوته در نواحی مختلف میباشد که با مقایسه با شعاع بوته در حالت نو میتوان ضخامت جداره را در آن ناحیه به دست آورد و راجع به تعمیر بوته تصمیم گرفت. برخی از تعمیرکاران کوره، قطر بوته را اندازهگیری میکنند که در مقایسه با اندازهگیری شعاع، دارای دقت کمتری است. به عنوان مثال اگر حد خوردگی چهار سانتیمتر باشد و قطر اندازهگیری شده شش سانتیمتر افزایش نسبت به حالت نو نشان دهد، نمیتوان دریافت که این ۶ سانتیمتر خوردگی به طور مساوی به دو طرف کوره تعلق داشته باشد (یعنی از هر طرف جداره سه سانتیمتر خورده باشد) چون این احتمال وجود دارد که مثلاً از یک طرف پنج سانتیمتر (یک سانتیمتر بیش از حد مجاز) و از طرف دیگر یک سانتیمتر (سه سانتیمتر کمتر از حد مجاز) خورده شده باشد. بنابراین وقتی فرصت اندازهگیری به وجود میآید، بهتر است شعاع بوته اندازهگیری شود تا اندازه بوته در هر ناحیه به دقت مشخص گردد. همراه با اندازهگیری شعاع یا قطر بوته در ارتفاعهای مختلف بوته، باید ارتفاع بوته را نیز اندازه گرفت تا اگر از حد مجاز فراتر رفته باشد، معلوم گردد. برای اندازهگیری شعاع بوته، یک شاقول در محل محور بوته آویزان میگردد و فاصله آن با جداره در نواحی مختلف اندازهگیری میشود و در جداول مخصوص یادداشت میگردد.
قسمت بالای کوره به خاطر برخورد شارژ جامد دائم در معرض صدمه قرار دارد. این قسمت نیز از طریق اندازهگیری و مشاهده مستقیم مرتباً کنترل میگردد.
نتیجهگیری
با ورود عناصر نیمههادی، صنعت کورههای القایی جهشی بزرگ را تجربه کرده و توانسته است محدودیتهای فرکانسی گذشته را پشت سر بگذارد. این پیشرفتها منجر به دستهبندی سیستمهای القایی به چهار دسته اصلی (منبع، موتور-ژنراتور، مبدل نیمههادی، و فرکانس رادیویی) شده که هر کدام با ویژگیهای فرکانسی و کاربردی خاص خود، طیف وسیعی از نیازهای صنعتی را پوشش میدهند.
کورههای ذوب القایی، بهویژه نوع بدون هسته، امروزه به دلیل راندمان بالا، محیط پاک، سرعت عمل، کنترل دقیق دما و توانایی همگنسازی مذاب، به گزینهای محبوب در صنایع فولادسازی، ریختهگری فلزات آهنی و غیرآهنی تبدیل شدهاند. این کورهها نیاز به الکترود گرافیتی ندارند و آلودگی صوتی کمتری ایجاد میکنند. اگرچه چالشهایی مانند فسفرزدایی و ظرفیت تولید پایینتر نسبت به کورههای قوس الکتریک وجود دارد، اما با استفاده از کورههای پاتیلی و آهن اسفنجی میتوان این محدودیتها را مدیریت کرد.
نکته کلیدی در بهرهبرداری بهینه از کورههای القایی، نگهداری دقیق و مستمر جداره نسوز است. پایش مداوم پارامترهای الکتریکی (جریان، ضریب توان، مقدار خازن) و اندازهگیری فیزیکی (شعاع و ارتفاع بوته) میتواند به شناسایی زودهنگام خوردگی یا ضخیم شدن جداره کمک کند و از توقفهای ناخواسته و کاهش راندمان جلوگیری نماید. پیشرفتهای اخیر در تأمین توان با فرکانس متغیر، طراحی القاگرها، بازیافت حرارت و اتوماسیون، در کنار ظهور کورههای القایی دوقلو، نویدبخش آیندهای روشنتر برای این تکنولوژی حیاتی در صنعت ذوب فلزات است. این کورهها با مزایای فراوان خود، ستون فقرات بسیاری از صنایع سنگین محسوب میشوند و پتانسیل بالایی برای توسعه و بهبود فرآیندهای تولید فلزات دارند.
الکترومارکت به عنوان یک منبع معتبر و تخصصی در حوزه تأمین تجهیزات اتوماسیون صنعتی، آماده ارائه خدمات جامع به شما عزیزان است. ما به شما کمک میکنیم تا بهترین تجهیزات را برای نیازهای خاص پروژه خود انتخاب کنید. خدمات ما شامل:
- مشاوره تخصصی رایگان: تیم مجرب مهندسان الکترومارکت آماده ارائه مشاورههای فنی دقیق برای انتخاب دقیقترین و مناسبترین درایو بر اساس مشخصات آسانسور شما هستند.
- تأمین و فروش: الکترومارکت تضمین میکند که شما سافت استارتر و اینورتر اصلی و با کیفیت را با بهترین قیمت و در کوتاهترین زمان ممکن دریافت خواهید کرد.
- پشتیبانی فنی و خدمات پس از فروش: حتی پس از خرید، میتوانید روی پشتیبانی فنی و خدمات پس از فروش ما برای نصب، راهاندازی، عیبیابی و رفع مشکلات احتمالی حساب کنید.
- منابع آموزشی و مقالات تخصصی: برای گسترش دانش خود در زمینه درایوها، PLC ها، HMI ها و دیگر تجهیزات صنعتی، میتوانید به طور منظم به وبلاگ الکترومارکت سر بزنید و از مقالات آموزشی ما بهرهمند شوید.